Rotary screw air compressors are widely used across industries due to their efficiency, reliability, and continuous operation capabilities. Understanding how these machines work helps users operate and maintain them effectively. In this article, we break down the working principle of rotary screw air compressors in a simple, clear, and professional way.
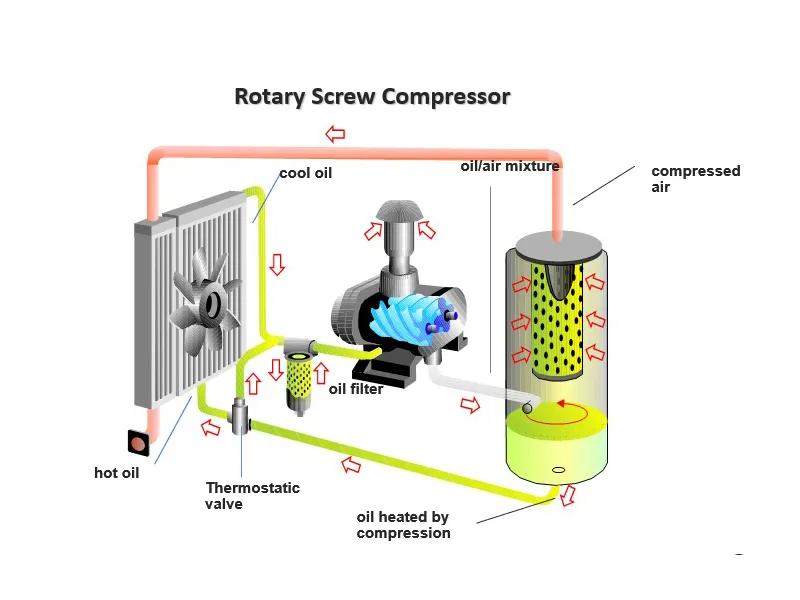
Contents
What Is a Rotary Screw Air Compressor?
A rotary screw air compressor is a type of positive displacement compressor that uses two meshing helical screws—commonly called rotors—to compress air. These compressors are known for delivering a constant flow of compressed air over long periods, making them ideal for industrial and commercial use.
There are two main types of rotary screw compressors:
- Oil-injected (or oil-lubricated) air compressors
- Oil-free air compressors
Both follow similar principles but differ in the way they manage lubrication and internal cooling.
Key Components
The main components of a rotary screw compressor include:
- Air End (Screw Element): The heart of the machine that compresses the air.
- Motor: Powers the screw elements.
- Inlet Valve: Controls the air entering the compression chamber.
- Oil Separator (for oil-injected types): Separates oil from compressed air.
- Coolers: Maintain optimal temperature levels.
- Control System: Manages compressor operation, load/unload cycles, and protection functions.
How Does It Work?
Step 1: Air Intake
When the compressor starts, atmospheric air enters through the inlet valve. This valve opens when the compressor is running in the “loaded” state and closes during idle or “unloaded” mode.
Step 2: Compression Process
Inside the air end, two rotors (male and female) rotate in opposite directions. As the rotors turn, air is trapped between the rotor lobes and the casing. This trapped air is gradually compressed as it moves along the length of the rotors.
- In oil-injected compressors, a thin layer of oil is also injected into the compression chamber. The oil acts as a lubricant, coolant, and sealant, significantly improving compression efficiency and durability.
- In oil-free compressors, there is no oil in the compression chamber. These designs use special coatings and materials to prevent wear and ensure clean air output.
Step 3: Discharge
Once the air reaches the end of the rotor chamber, it is at a much higher pressure than when it entered. The compressed air is then discharged into the air receiver or directly to the distribution system.
Step 4: Cooling and Separation (for Oil-injected Units)
In oil-injected models, the compressed air and oil mixture exits the air end and enters the oil separator tank. Here, oil is separated from the air using mechanical and filtration methods. The recovered oil is cooled and recirculated back into the system.
The compressed air is also passed through an aftercooler to lower its temperature before it moves on to the application point.
Load and Unload Mode
Rotary screw compressors typically run in two modes:
- Load Mode: The inlet valve is open, and the compressor is actively producing compressed air.
- Unload Mode: The inlet valve is closed, and the compressor runs without producing air, waiting for pressure to drop before switching back to load mode.
This cycling allows the compressor to save energy and reduce wear during low-demand periods.
Advantages of Rotary Screw Compressors
- Continuous Operation: Ideal for 24/7 operations.
- Energy Efficiency: Maintains a steady airflow with minimal pressure fluctuation.
- Low Maintenance: Fewer moving parts compared to piston compressors.
- Quiet Operation: Quieter than traditional reciprocating compressors.
- Compact Design: Space-saving with integrated systems.
Applications
Rotary screw compressors are used in a wide range of industries, including:
- Manufacturing
- Automotive
- Food and Beverage
- Pharmaceuticals
- Electronics
- Packaging
Their ability to provide clean, consistent air makes them suitable for both general industrial use and sensitive applications requiring oil-free air.
Final Thoughts
Rotary screw air compressors are a cornerstone of modern compressed air systems. Their working principle—based on efficient, continuous compression using rotating screws—makes them ideal for demanding operations. Whether you choose an oil-injected or oil-free model, understanding how it works helps ensure proper usage, energy savings, and long-term reliability.