The Air End is often called the heart of the compressor. That’s because it is where the actual compression takes place. Other terms for the Air End are the compressor element or compressor stage.
Air Ends come in different types, depending on the technology and physical principle. The two main principles of compression are: positive displacement and dynamic compression. Positive displacement refers to compression by reducing the air volume. Technologies that use this principle are pistons, scrolls, and tooth or screw rotors. Dynamic compression uses centrifugal – or turbo – technology to compress air or gas by changing its speed.
Contents
- 1 1. Introduction: Defining the Air Compressor System and the Role of Its Components
- 2 2. Key Functions of the Air End: Examining Its Role in Different Compressor Types
- 3 3. Direct Impact of the Air End on Compressor Performance
- 4 4. Energy Consumption and Air End Condition
- 5 5. Lifespan and Failure Rates Associated with the Air End
- 6 6. Critical Maintenance Requirements for the Air End
- 7 7. Comparison of the Air End with Other Important Components
- 8 8. Conclusion: Reinforcing the Argument for the Air End as the Most Critical Component
- 9 9. Reference
- 10 Related Products
1. Introduction: Defining the Air Compressor System and the Role of Its Components
An air compressor system is an electromechanical device that converts energy into the potential energy of compressed air, which serves as a versatile power source across a wide range of industrial, commercial, and even residential applications. A typical air compressor system comprises several interconnected components, each playing a vital role. These components include:
The air end, which serves as the core compression mechanism responsible for compressing the air; the prime mover, typically an electric motor or an internal combustion engine, which provides the mechanical power needed to drive the air end.
The control system, encompassing sensors, controllers, and software, used to regulate the compressor’s operation, ensuring that compressed air demands are met while optimizing efficiency and safety;
Air treatment components, such as inlet filters, oil separators (for lubricated compressors), aftercoolers, moisture separators, air dryers, and downstream filters, which are essential for removing contaminants and moisture from the compressed air to meet the requirements of specific applications;
The air receiver tank (receiver), which acts as a buffer, storing compressed air to accommodate fluctuating demands and stabilize system pressure.
The distribution network, consisting of pipes, valves, and fittings, which delivers the compressed air from the compressor to the points of use. To fully appreciate the paramount importance of the air end, it is first necessary to recognize the interplay of these components within the broader system.
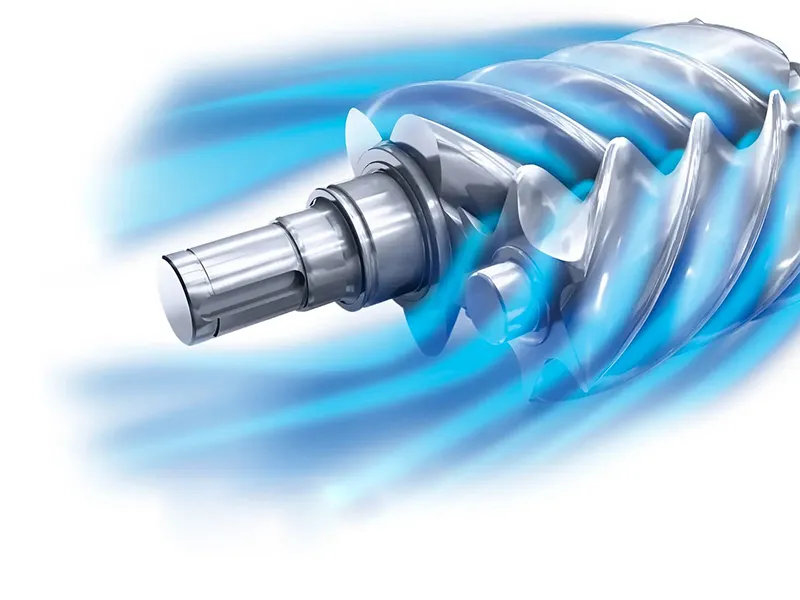
While the efficient and reliable operation of an air compressor system depends on the proper functioning of all its constituent parts, the air end holds a uniquely critical position within it. It is the direct embodiment of the system’s primary function—the transformation of ambient air into a usable form of energy through compression. The design, efficiency, and condition of the air end have a profound and direct impact on the overall performance, energy consumption, and lifespan of the entire air compressor system. Without a properly functioning air end, the system fundamentally cannot achieve its intended purpose of providing compressed air, regardless of the state of the other components.
Insight 1: The Air End as the “Heart” of the System – Reasoning Process:
Numerous authoritative sources within the compressed air industry and technical literature explicitly refer to the air end as the “heart” of a screw compressor. This metaphorical designation is not merely figurative; it reflects the indispensable role the air end plays in the system’s operation.
- The heart in a biological system is the central organ responsible for pumping blood, which is essential for delivering oxygen and nutrients to all other parts of the body, enabling them to function.
- Similarly, the air end in a compressor system is the core component responsible for “pumping,” or more accurately, compressing air, which is the lifeblood of pneumatic systems, powering various tools and processes.
- Just as heart failure leads to the cessation of bodily functions, a catastrophic failure or severe inefficiency of the air end renders the entire compressor system incapable of performing its primary task of supplying compressed air.
- Therefore, likening the air end to the “heart” underscores its fundamental and irreplaceable role, highlighting its criticality above other supporting components.
2. Key Functions of the Air End: Examining Its Role in Different Compressor Types
- Rotary Screw Compressors:
- Working Principle: Rotary screw compressors are a type of positive displacement compressor that achieve air compression through the action of two precisely engineered, intermeshing helical rotors (a male rotor with convex lobes and a female rotor with corresponding concave flutes) rotating within a stator housing. As these two rotors turn in opposite directions, air is drawn into the inlet port and becomes trapped in the progressively decreasing volume between the rotors and the stator, causing a corresponding increase in pressure before being expelled through the discharge port.
- Oil-Flooded vs. Oil-Free: Rotary screw compressors are primarily available in two configurations:
- Oil-flooded (or oil-injected) compressors inject oil into the compression chamber. This oil serves several critical functions: lubricating the rotors and bearings, carrying away the significant heat generated during compression, and forming a tight seal between the rotors and the housing, thereby enhancing efficiency.
- Oil-free (or oil-less) compressors are designed to compress air without the introduction of oil into the compression chamber. These types typically employ sophisticated seals, coatings, and sometimes water injection for sealing and cooling, ensuring the delivery of oil-free air.
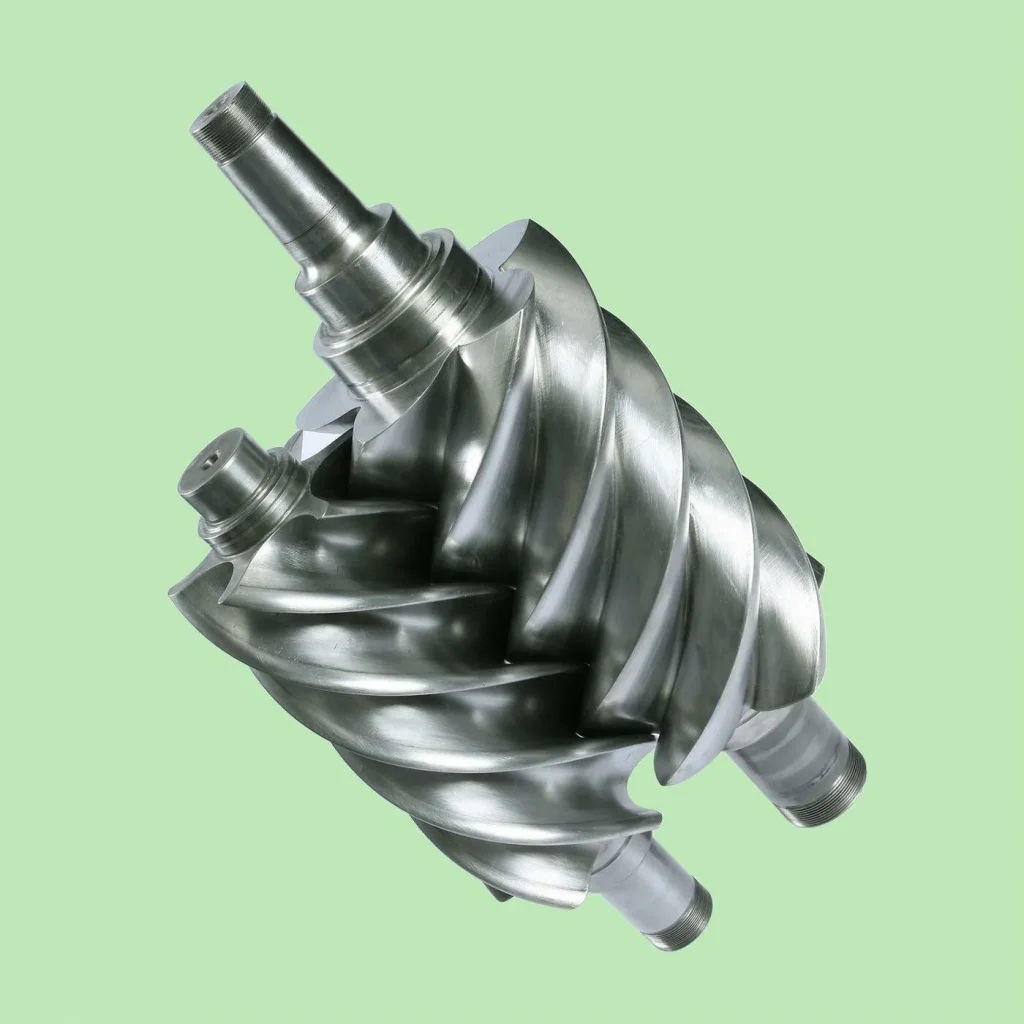
- Reciprocating Compressors:
- Working Principle: Reciprocating compressors are another type of positive displacement machine that utilizes the back-and-forth motion of a piston within a cylinder to compress air. During the intake stroke, the piston moves away from the cylinder head, drawing air into the cylinder through an inlet valve. On the compression stroke, the piston moves towards the cylinder head, reducing the volume of the trapped air and increasing its pressure. The high-pressure air is then discharged through an outlet valve. These compressors can be single-acting (compressing air on only one side of the piston) or double-acting (compressing air on both sides), and they can operate in single or multiple stages to achieve different pressure levels.
- Centrifugal Compressors:
- Working Principle: Centrifugal compressors belong to the class of dynamic compressors, employing a different method of air compression than positive displacement types. They utilize a high-speed rotating disk or impeller within a shaped housing to increase the kinetic energy of the incoming air. Air is drawn into the center of the impeller and accelerated radially outwards by centrifugal force, significantly increasing its velocity. This kinetic energy is then converted into pressure energy as the high-velocity air is decelerated in a diffuser section (a divergent duct) located downstream of the impeller. Centrifugal compressors are primarily used in applications requiring continuous, high-flow, moderate-pressure air.
- Scroll Compressors:
- Working Principle: Scroll compressors are another type of positive displacement compressor that achieves air compression through the interaction of two intermeshing spiral-shaped elements, known as scrolls. Typically, one scroll is fixed, while the other orbits eccentrically within it without rotating. This orbital motion traps pockets of air between the two scrolls. As the orbiting scroll moves around the fixed scroll, the volume of these trapped air pockets progressively decreases, leading to a continuous increase in pressure until the compressed air is discharged from the center of the scroll set. Scroll compressors are known for their smooth, quiet, and reliable operation, particularly in lower-capacity applications.
- Insight 2: The Air End as the Site of Compression – Reasoning Process:
- Across the various air compressor technologies, a consistent theme emerges: the air end stands as the central and indispensable component where the fundamental physical process of compressing air takes place.
- Reasoning Process:
- In screw compressors, the intermeshing rotors within the air end directly reduce the volume of air.
- In reciprocating compressors, the movement of the piston within the air end’s cylinder achieves compression.
- In centrifugal compressors, the impeller within the air end imparts velocity to the air, which is then converted to pressure.
- In scroll compressors, the orbiting and fixed spirals within the air end progressively compress the trapped air.
- Regardless of the specific mechanism employed, the act of compression invariably occurs within the air end, underscoring its unique and critical function. The air end is not merely a supporting component; it is the very heart of the air compression process.
3. Direct Impact of the Air End on Compressor Performance
- Efficiency:
- The efficiency of an air compressor, defined as the ratio of useful compressed air output to energy input, is profoundly influenced by the design and condition of the air end. A well-designed and properly maintained air end minimizes energy losses during the compression process.
- An efficient air end requires less motor power to produce a given volume of compressed air at the desired pressure, directly translating to lower operating costs. Conversely, inefficiencies within the air end, such as increased internal leakage due to wear or improper clearances, or increased friction due to inadequate lubrication, necessitate the motor consuming more energy to achieve the same output.
- Reliability:
- The air end is often the most stressed component within a compressor, as it endures high pressures and continuous operation, making its condition a key determinant of the compressor’s reliability.
- Mechanical failures within the air end, such as bearing failures and rotor damage in screw compressors, piston ring wear in reciprocating compressors, or impeller damage in centrifugal compressors, can lead to sudden and costly compressor downtime. Conversely, diligent and proactive maintenance of the air end is crucial for ensuring the sustained reliable operation of the entire compressor system.
- Overall Output (Flow and Pressure):
- The design specifications and operational condition of the air end directly dictate the volume (in cubic feet per minute, or CFM) and pressure (in pounds per square inch, or PSI) of compressed air that the system can deliver—the fundamental output characteristics of an air compressor system.
- A worn air end may struggle to achieve the required pressure or flow rate, impacting the performance and efficiency of downstream equipment that relies on the compressed air supply.
- Insight 3: The Air End as the Primary Determinant of Performance – Reasoning Process:
- The overall performance of an air compressor system—encompassing its energy conversion efficiency, the reliability of its continuous operation, and its ability to deliver the required volume and pressure of compressed air—is inextricably linked to the air end.
- Reasoning Process:
- While the motor provides the power, the air end is the mechanism that transforms this power into compressed air with specific flow and pressure characteristics.
- The control system manages the operation, but the air end’s capabilities define the limits of performance.
- Air treatment components optimize the output, but they cannot function without the initial compressed air produced by the air end.
- Therefore, the air end is the primary determinant of whether a compressor system can effectively and economically meet the demands of its intended application.
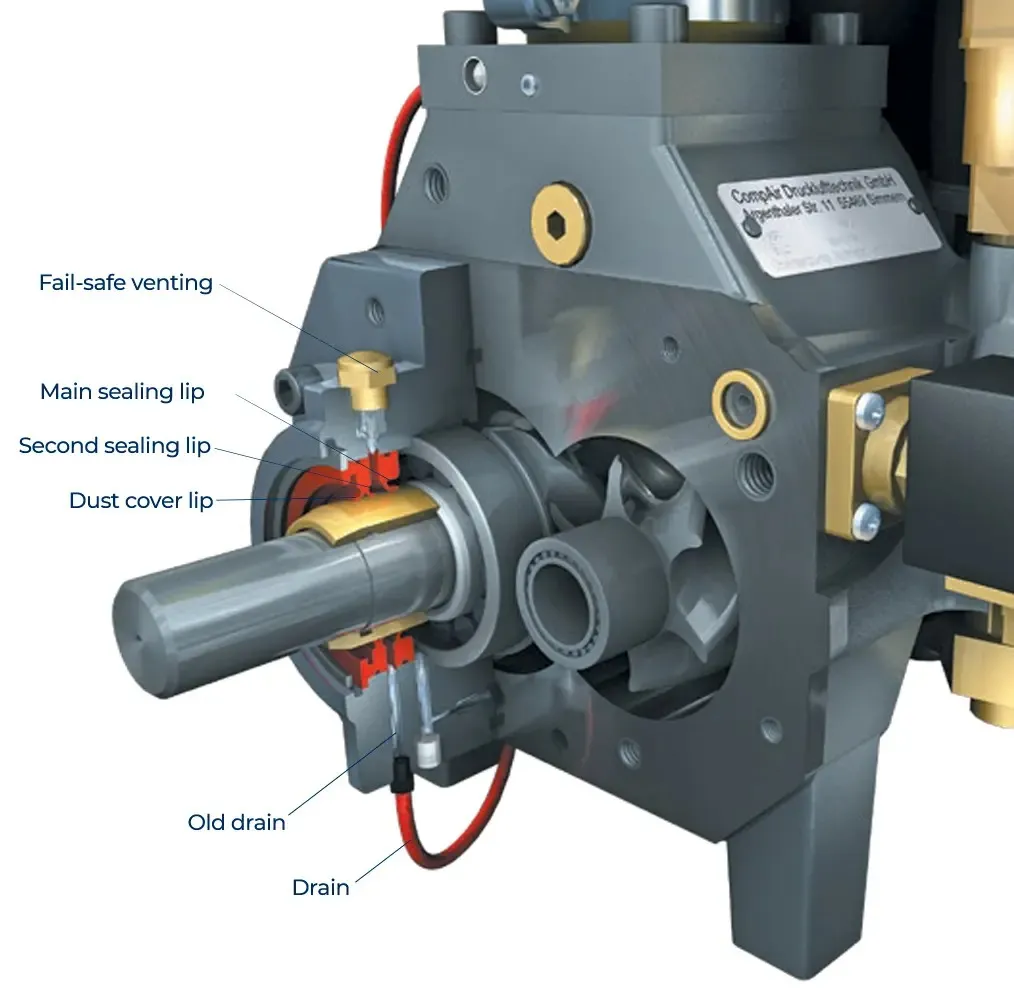
4. Energy Consumption and Air End Condition
- Direct Link Between Air End Efficiency and Energy Costs:
- An inefficient air end requires more energy to compress air, leading to higher electricity bills, which constitute a significant portion (70-80%) of the total cost of ownership. A worn air end can result in a noticeable increase in energy consumption.
- Quantifying the Impact:
- Studies indicate that optimizing compressed air systems can achieve energy savings of 20-50%.
- A pressure drop of 10 PSIG caused by improper filter maintenance can lead to a 5% increase in energy costs.
- For systems operating around 100 psig, every 10 psig increase in pressure results in approximately a 5% increase in energy consumption at full load.
- Heat Generation and Energy Loss:
- Approximately 90% of the energy used to produce and distribute compressed air is lost, primarily as heat. The air end is the primary source of this heat generation during the compression process. An inefficient air end may generate even more heat, further contributing to energy waste and potentially requiring additional cooling.
- Insight 4: The Air End as a Major Contributor to Energy Consumption – Reasoning Process:
- Given that electricity costs represent the largest component of an air compressor’s life cycle cost and that the air end’s efficiency directly dictates the energy required for compression, the air end plays a pivotal role in the system’s overall energy consumption. An inefficient or poorly maintained air end can be a significant drain on energy resources, highlighting the economic imperative of ensuring its optimal condition.
5. Lifespan and Failure Rates Associated with the Air End
- Typical Lifespan:
- The expected operational lifespan of an air end is a critical consideration for the overall economics and reliability of an air compressor system. This lifespan can vary significantly depending on the specific type of compressor technology, the severity of the operating conditions, and, most importantly, the diligence of the maintenance practices employed.
- Rotary screw air ends, known for their robust design and suitability for continuous operation, can typically achieve a lifespan of 40,000 to over 100,000 operating hours under proper maintenance, which can translate to 10 years or more.
- Reciprocating air ends, often found in applications with intermittent operation, generally have a shorter expected lifespan, around 50,000 operating hours.
- Centrifugal air ends, designed for high-capacity, continuous industrial use, boast the longest potential lifespan, often exceeding 250,000 operating hours.
- Factors Affecting Lifespan:
- Maintenance is the most significant factor determining the lifespan of an air end. Consistent and meticulous maintenance practices, including adhering to manufacturer-recommended lubrication schedules, regularly replacing air and oil filters, and promptly addressing any signs of wear or malfunction, are crucial for maximizing the operational life of the air end.
- Operating conditions, such as ambient temperature, the level of dust and other contaminants in the intake air, and ambient humidity, can also significantly impact the lifespan of the air end [2, 1, , , ]. Harsh operating environments can accelerate the wear and tear of internal components.
- The inherent quality of the air end itself, including its design, the materials used in its construction, and the precision of its manufacturing, is a fundamental determinant of its long-term durability and resistance to failure.
- Percentage of Compressor Failures Attributed to Air End Issues:
- While the research snippets do not provide a precise percentage of compressor failures directly attributable to air end issues that is universally applicable, multiple sources consistently indicate that problems within the air end are a common cause of compressor failure.
- Specific failure modes within the air end, such as bearing failures, rotor damage in screw compressors, piston ring wear in reciprocating compressors, and impeller damage in centrifugal compressors, are frequently cited as primary reasons for compressor breakdowns and the need for repair or replacement.
- The fact that rebuilding the air end is often considered a more economical alternative to replacing the entire compressor unit strongly suggests that the air end is a critical point of failure requiring specialized attention to maintain the overall health of the compressor system.
- Insight 5: The Air End as a Common Point of Failure – Reasoning Process:
- The typical lifespan data for air ends, coupled with the repeated mention of air end issues as a common cause of compressor failures , strongly suggests that the air end, due to its complex mechanical design and the demanding conditions under which it operates at high stress, is a particularly vulnerable component within an air compressor system.
- Reasoning Process:
- The air end is the primary working element directly involved in the high-stress process of air compression.
- This continuous operation under high pressure and often elevated temperatures leads to inherent wear and tear on its internal components.
- The complexity of the air end, with its tight tolerances and multiple moving parts, increases the likelihood of mechanical issues arising.
- The industry practice of rebuilding air ends indicates that failures within this component are common enough to warrant specialized repair procedures.
- Therefore, while other components can also fail, the air end’s central role and the stresses it endures make it a significant contributor to the overall failure rate of an air compressor system.
6. Critical Maintenance Requirements for the Air End
- Lubrication:
- Maintaining proper lubrication within the air end is crucial for its efficient operation and extended lifespan, particularly in rotary screw compressors. Lubricants serve to cool, seal, and reduce wear between moving parts, thereby minimizing friction and preventing overheating.
- Adhering to the manufacturer’s recommended lubrication schedule, including regular oil changes and the use of specified lubricant types, is essential. Using the wrong type or grade of lubricant, or neglecting timely changes, can lead to accelerated wear, increased operating temperatures, and ultimately premature air end failure.
- Cooling:
- Effective cooling of the air end is vital for sustaining optimal performance and preventing damage from overheating. The compression process generates significant heat, and if this heat is not adequately dissipated, it can lead to lubricant degradation, increased wear, and reduced efficiency and lifespan of the air end.
- Maintenance practices aimed at ensuring proper cooling include verifying adequate ventilation around the compressor unit and regularly cleaning any cooling fins or heat exchangers associated with the air end. Obstructions or buildup of dust and debris on these cooling surfaces can impede heat transfer, leading to elevated operating temperatures within the air end.
- Inspection:
- Regular visual and operational inspections of the air end are crucial for early detection of potential issues. This includes checking for signs of lubricant leaks, listening for unusual noises or vibrations emanating from the air end, and monitoring operating parameters such as discharge pressure and temperature.
- Deviations from normal operating conditions can be early indicators of underlying problems within the air end, which, if addressed promptly, can prevent more severe damage and extend the component’s lifespan.
- Filter Replacement:
- Keeping air and oil filters clean is essential for preventing contaminants from entering the air end and ensuring its optimal performance. Dust, dirt, and other particulate matter in the intake air can act as abrasives, accelerating wear on internal air end components. Similarly, contaminants in the lubricant can reduce its effectiveness and lead to increased friction and heat generation. Therefore, regular replacement of these filters according to the manufacturer’s recommendations is critical.
- Rebuilding vs. Replacement:
- Despite diligent maintenance, air ends have a finite lifespan and may eventually require rebuilding or complete replacement. Rebuilding typically involves disassembling the air end, inspecting its internal components for wear or damage, replacing worn parts such as bearings and seals, and then reassembling and testing the unit.
- In many cases, rebuilding an air end can be more cost-effective than replacing the entire compressor, highlighting the air end’s importance as a repairable core component. The decision to rebuild or replace often depends on the extent of the damage, the age of the compressor, and a cost-benefit analysis.
- Insight 6: Specialized Maintenance for a Critical Component – Reasoning Process:
- The specific and often technically demanding maintenance procedures required for the air end —including specialized lubrication, cooling considerations, and the potential for rebuilding—underscore its unique and critical nature.
- Reasoning Process:
- The air end’s internal mechanical structure involves tight tolerances and high-speed movements, necessitating precise lubrication and cooling regimes.
- The need for regular, thorough inspections, often requiring specialized knowledge to interpret operating parameters and identify subtle signs of wear, highlights its complexity.
- The option of rebuilding the air end, rather than simply replacing it, indicates its value as a core, repairable component, unlike more readily replaceable parts.
- This specialized maintenance required for the air end, compared to the maintenance of more generic components, further solidifies its status as the most critical element for the sustained performance and longevity of the air compressor system.
7. Comparison of the Air End with Other Important Components
- Motor:
- The motor provides the power to drive the air end. Without a functioning motor, the air end cannot operate. However, even with a perfectly functioning motor, no compressed air can be produced without a properly working air end. The air end is the component that directly performs the compression, making it the primary working element. The motor’s role is to enable the air end to function.
- Insight 7: The Motor as the Enabler, the Air End as the Performer – Reasoning Process: While the motor is essential for driving the compressor, its function is to provide mechanical energy. The air end is the component that utilizes this energy to perform the core task of air compression. Therefore, the air end is arguably more critical to the system’s output as it is directly involved in the primary function.
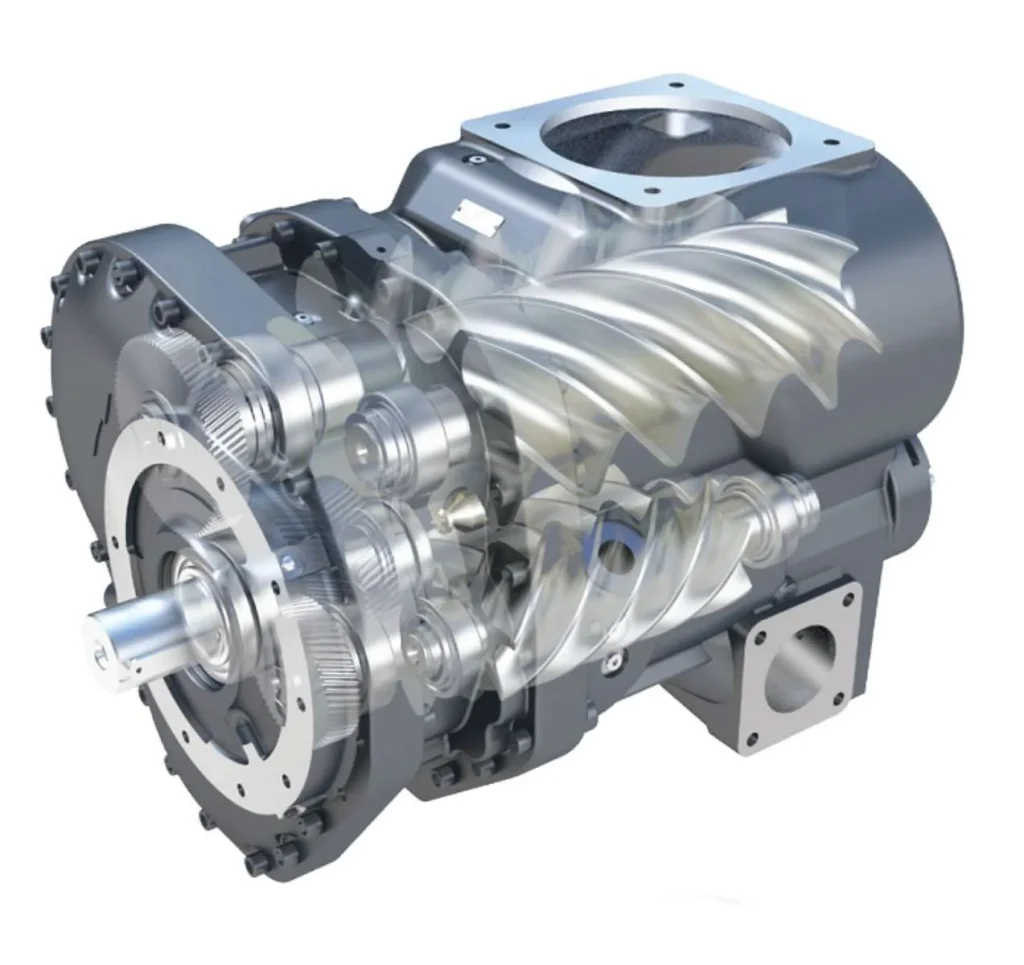
- Control System:
- The control system manages the compressor’s operation, including starting, stopping, regulating pressure, and ensuring safety. A malfunctioning control system can lead to inefficient operation or even compressor failure. However, even with a perfectly functioning control system, a damaged or non-operational air end will prevent the system from producing compressed air. The control system optimizes the operation of a working compressor, but it cannot compensate for a failed air end.
- Insight 8: The Control System Optimizes, the Air End Generates – Reasoning Process: The control system is vital for ensuring the efficient and safe operation of the compressor. However, its role is secondary to the air end’s primary function of generating compressed air. If the air end is not functioning correctly, even a sophisticated control system cannot produce compressed air.
- Air Treatment Components (Filters, Dryers):
- Air treatment components remove contaminants and moisture from the compressed air, ensuring air quality and protecting downstream equipment. Their failure can lead to product contamination or damage to pneumatic tools. However, these components operate after the air end has produced the compressed air. Without a functioning air end, there is no compressed air to treat.
- Insight 9: Air Treatment Enhances Output, the Air End Creates Output – Reasoning Process: Air treatment components are essential for ensuring the quality of the compressed air. However, they are located downstream of the air end and rely on the air end to produce the initial compressed air. Therefore, the air end’s role in the fundamental process precedes and is arguably more critical than that of air treatment.
8. Conclusion: Reinforcing the Argument for the Air End as the Most Critical Component
- The air end is the core component of any air compressor system, the sole element responsible for performing the fundamental process of air compression.
- Its efficiency and condition directly and significantly impact the system’s performance, energy consumption, reliability, and output.
- Compared to other important components such as the motor, control system, and air treatment, the air end’s function is primary and indispensable to the very purpose of an air compressor system.
- Proper maintenance and timely repair or replacement of the air end are paramount for ensuring the long-term, efficient, and reliable operation of the entire compressed air system.
- The criticality of the air end lies in its direct influence on operating costs, the risk of failure leading to significant downtime, and its role as the ultimate determinant of the compressed air output that powers a multitude of applications.
9. Reference
- How Does an Air Compressors Work?
- What Is An Air Compressor Air End?
- If the Compressor Air End is worn or damaged, can it be refurbished?
Related Products
-
1616747281 Air End for Atlas Copco ZR ZT Air Compressor
$2,965.00 – $3,000.00 -
1616770780 Air End for Atlas Copco Air Compressors
$7,500.00 – $8,500.00 -
Air End 1616747281=1616679281 for Atlas Oil-free Compressors
$15,000.00 – $50,000.00 -
Air End 1616869380 1616869390 For Atlas Copco
$800.00 – $1,800.00